From Indian hands to your home. The craft behind Our Storage Bags
Long before Hayden Hill began, our founders were serving customers in the marketplace through other businesses. And, as they interacted with their customers, they saw how frustrated people were that they had to store their most precious garments in cheaply made plastic bags which soon fell apart, left their valuable clothing vulnerable to damage, and had limited view of the garments inside. A functional, high-quality, sustainably sourced clothes storage bag did not exist. So our founders - Adam and Karol - began dreaming of ways to create something entirely different - quality storage products made from quality materials that didn't harm the environment or the workers who made them. Achieving this goal was not as easy as we originally thought. We were adamant that we would not use traditional manufacturing practices in which items are mass-produced, low quality, and made by people under poor working conditions.

Protecting The Environment As Well As Your Clothes
The first step was to find the right manufacturers, and our sourcing partners in India helped us begin the search. Our partners only work with third-party certified factories that use environmentally friendly materials and provide good working conditions. The factories that met our criteria were located in southern India, a hub of textile production.
We were thrilled to find the right manufacturing partners, but another challenge arose - they had never made a similar product. Because neither of us had made a product like this, we were all learning together, and we tested many samples.
We experimented and refined the sample bags until we had a product that was ready for our customers. It was a year in the making from the initial sketch to the finished product. One of the key improvements was creating a see-through side panel so that our Hayden Hill customers can view all the items stored in their hanging garment bags and clothes storage bags.
But, before launching our luxurious garment bags, it was important for us to visit our Southern India partners in person.
Founder Karol Caballero said, “We wanted to see for ourselves that the ethics were there, that we were being true to our ethos. We needed to know that the people [workers] wanted to be there and were being treated well.”
So, in May 2022, the Hayden Hill team traveled to India to experience the journey our bags take from seed to shipping.

Our Products’ Journey
Cotton Farm
Karur, India
When our team arrived at the organic cotton farm, we were warmly greeted by a small team of hard-working farmers. There were two men in charge of the crop – an older man who looks after the cotton fields through the seasons, and his son.
He said they “treat the crops like their children,” watching and determining what they need to grow best. The farmers decide how much water and which natural fertilizer the cotton needs. They ensure the soil is healthy and rich, and there is no disease.
Cotton plants take 150 days to grow before they are ready to be picked. Each year, the farmers purchase locally grown cotton seeds from another local farm and prepare the soil for planting. They test the soil to determine what it needs to create the perfect environment for cotton to grow.
In January, the farmers plant the seeds and wait 10 days for them to germinate. Cotton plants produce buds before developing white flowers, which later turn pink. After the flowering stage, the cotton plant produces a boll. When the boll has grown to full size and maximum weight, it opens and exposes the fluffy cotton within. Then, it's time to harvest the cotton.
After the cotton is harvested, it is sent to a nearby factory to be cleaned.
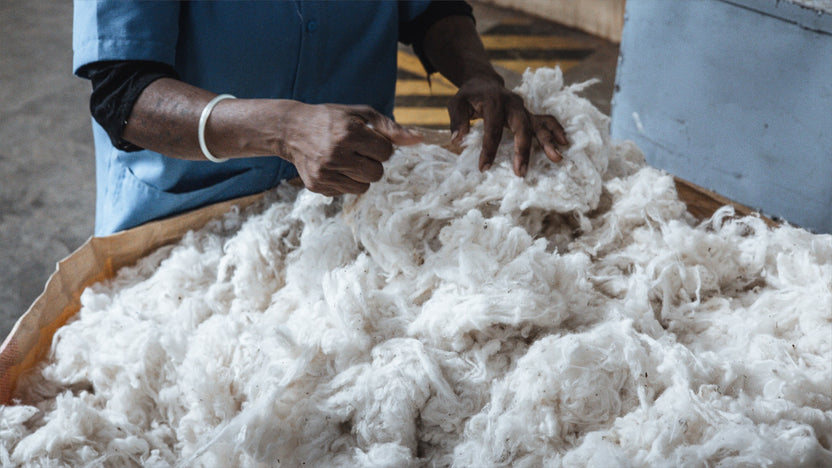
Cleaning
Karur, India
Cotton brings to mind white, fluffy balls, but that is not at all what raw cotton looks like. It is brown in appearance and must go through hours of cleaning to remove any seeds and dirt.
As you can imagine, this process requires significant amounts of water. But because our partners share our desire to protect the environment, the factory sends this brown, dirty water through a recycling process. The end result is clear, clean water that can be used to wash another batch of dirty, raw cotton. The batches of cleansed cotton are gathered and sent to the next factory to be spun and weaved into fabric.

Spinning and Weaving
Coimbatore, India
At this factory in Coimbatore, machinery is used to spin the cleaned cotton into fibers. Spinning wheels pull these cotton fibers apart and spin them to form thread. A weaving mill takes the threads and weaves them into fabric. Workers examine the finished fabric to search for any flaws. Then, the cotton fabric travels to the city of Karur to be steamed and dyed.

Steaming and Drying
Karur, India
The woven fabric has a beige color and must be steamed to become white. This steaming process involves placing the fabric in a roller and washing it with water and eco-friendly chemicals for 10 hours. Steaming also utilizes a significant amount of water. Conventional manufacturing processes often pump dirty, chemically treated water into the ground, but this factory recycles its water using an extensive system.
The water is pumped to six different cement blocks to clean the water. Each cement block has its own pump that extracts the dirt from the water. Due to the intense cleaning of the cotton, the water must go through this process of removing dirt six times to achieve clarity and restore the water to drinking form.
At the end of the process, sludge with a mud-like consistency is left at the bottom of the deposit tank. This sludge is bagged and sent to construction plants to make cement. The cleansed water is used to clean the next batch of cotton, and the cycle begins again. Absolutely no waste is produced.
The cleaned cotton is then steamed and placed into a large machine, about 200 feet in length, to be dried and prepared for transport to the next stage.

Assembly
Karur, India
The textile factory in Karur is where cotton fabric is crafted into Hayden Hill garment bags. The fabric goes through several steps at this factory. It is:
- Cut using a pattern
- Sewn together to create the bag's shape
- Supplemented with trim and zippers
- Accented with leather detachable zipper pulls
- Checked for quality and measured for accuracy
- Ironed to a pristine condition
- Packaged into bags and shipped to Hayden Hill
Our team was able to watch our bags be assembled and witness the workers' precision and skill.
Our sourcing partners, who planned our tour of the farm and factories, and served as our tour guides during the trip said, “We've never had anyone we work with care or want to see the whole process.”

Social Sustainability
In addition to visiting the places our products are made, it was incredibly important to our Hayden Hill team to see for ourselves that those involved in the making of our products are treated fairly, earn a liveable wage, and have good working conditions.
As a part of obtaining our GOTS certification, our team provided a significant amount of documentation proving that our workers were being treated well. The GOTS Standard protects the well-being of workers– that their working hours are reasonable, the working environment is safe and comfortable, breaks are given, and that they are not harassed or discriminated against.
But, having documentation that workers were being treated fairly and witnessing it for ourselves were two different things. We wanted to personally meet the workers.
And, we were so glad we did. The factories are actually quite small. The assembly unit in Karur employs about 30 employees who help create Hayden Hill products. The factory itself is immaculate; everyone who goes into the factory removes their shoes and wears masks and hair nets to keep the products clean.
Many of these workers are in their 30s, with the men stitching and sewing, and the women doing final product inspections. We were amazed at how friendly the people were; they all wanted to take photos with us. They seemed happy, content with their work, and had plenty of breaks.
The factory owner mentioned,
“None of the people at the other companies we work with ever speak or make eye contact with the workers. You guys actually care.”

Giving Back
Another part of our ethos at Hayden Hill is supporting the region in which our product is made. So, while we were in India, our team visited an orphanage that was close to our founders’ hearts. The orphanage is located in Karur and can house up to 100 boys and girls from ages 5 to 14. The children eat, sleep, have lessons, and play at the orphanage. The boys' and girls' spaces are separated by a courtyard where the children play and exercise.
Hayden Hill provided a special meal from a local restaurant and some play equipment for the children, but the children were most excited about having visitors and playing with us. We had so much fun and even had a hula hoop contest with them.
Our creative and social media manager India Hodder said, “We had a great day visiting the children. It was humbling to see how happy they were, and it made me realize how much we take for granted. The children were fascinated with my name [India] and kept touching my skin and hair. It was rewarding to drive away from here knowing that our visit was a positive experience for them.”
We are now developing an ongoing support package for the orphanage and are honored to be able to reinvest in the local community that is making our dream possible.
Visiting the orphanage was one of the highlights of our trip to Southern India.
“When buying from Hayden Hill you know that you are investing in our core values that people matter, giving back is important, and reducing our impact on the environment is the way forward.”
Frequently Asked Questions
Hayden Hill partners with Indian communities to create high-quality, sustainable clothing storage solutions. By working directly with skilled artisans, we ensure fair working conditions and support local economies. Our products are made from ethically sourced, premium cotton, reflecting our commitment to both quality and environmental responsibility.
Hayden Hill considers our Southern Indian partners to be exactly that, and fostering growth and a better quality of life in these local communities is a big part of our passion, and responsibility, as a sustainable company. At Hayden Hill, we have close relationships with local communities, orphanages, and charities where our products are made, as well as our Hayden Hill foundation; which aims to elevate the lives of women in India by providing them with expense-paid education and greater opportunities to achieve later in life.
Hayden Hill is committed to sustainability and ethical practices. Our products are made from 100% organic cotton, sourced and processed locally in India. From handpicking to assembly, our process prioritizes eco-friendly methods and fair labor. Our GOTS-certified factories provide safe, supportive working conditions for our skilled artisans, ensuring they receive fair wages and benefits.
The Hayden Hill Foundation is a new organization that was formed very recently by us, that is dedicated to promoting the professional and social development of women in India. As a secondary arm to the Hayden Hill name, the foundation serves as an extension of our desire to not only partner with the right people in a sustainable way, but to also lift up those in the local communities of Southern India, and provide them with more opportunities and a greater quality of life. The main responsibilities of the Hayden Hill Foundation are to help women of all ages in India to achieve greater things, find more professional and social opportunities, acquire access to a better standard of education, and more. You can learn more about what the Hayden Hill Foundation aims to do here.
If your question is not answered here, please check out our FAQ page.
read more faqs